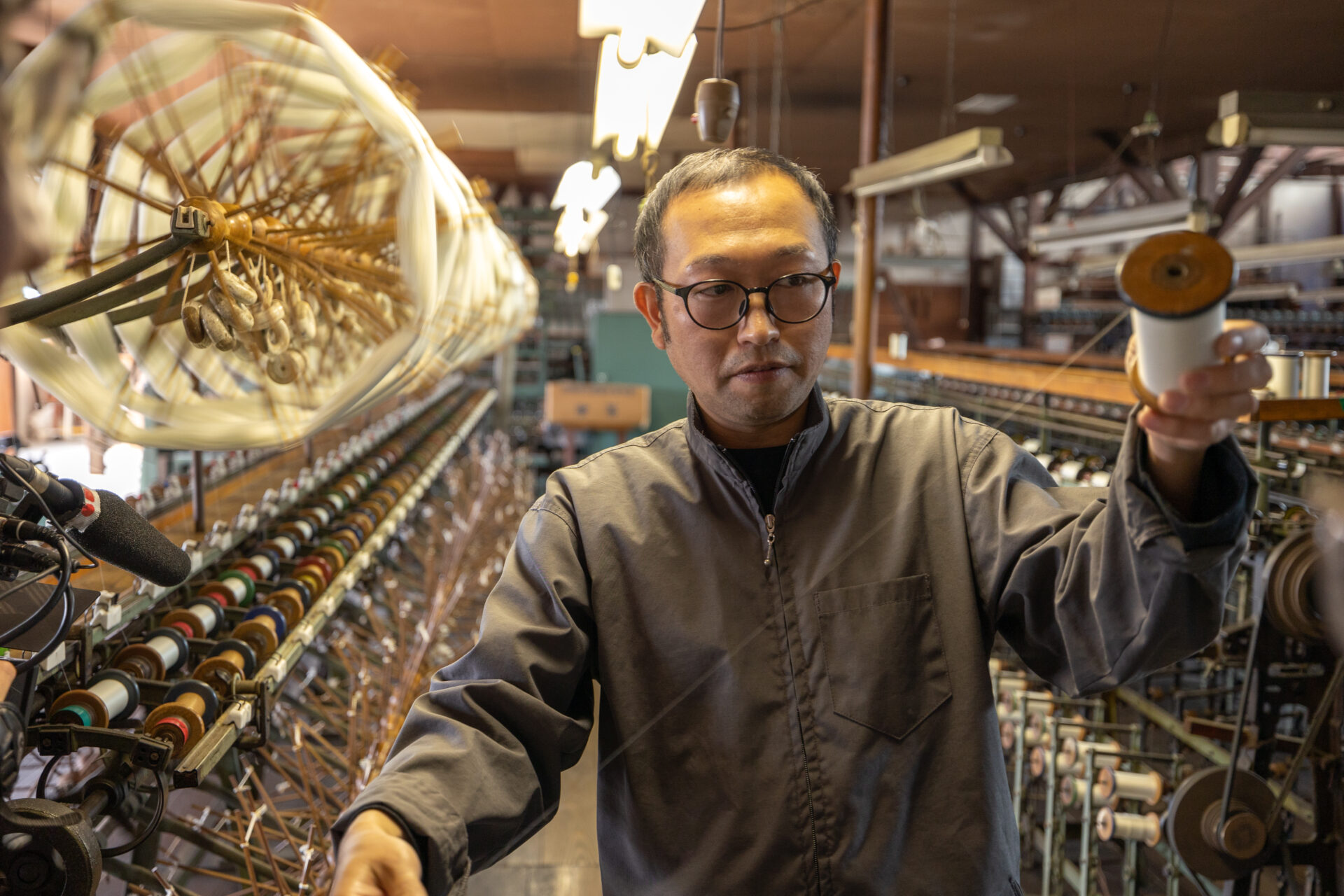
Preserving Valuable Traditions for the Future as the Sole Weaver of Local Memories.
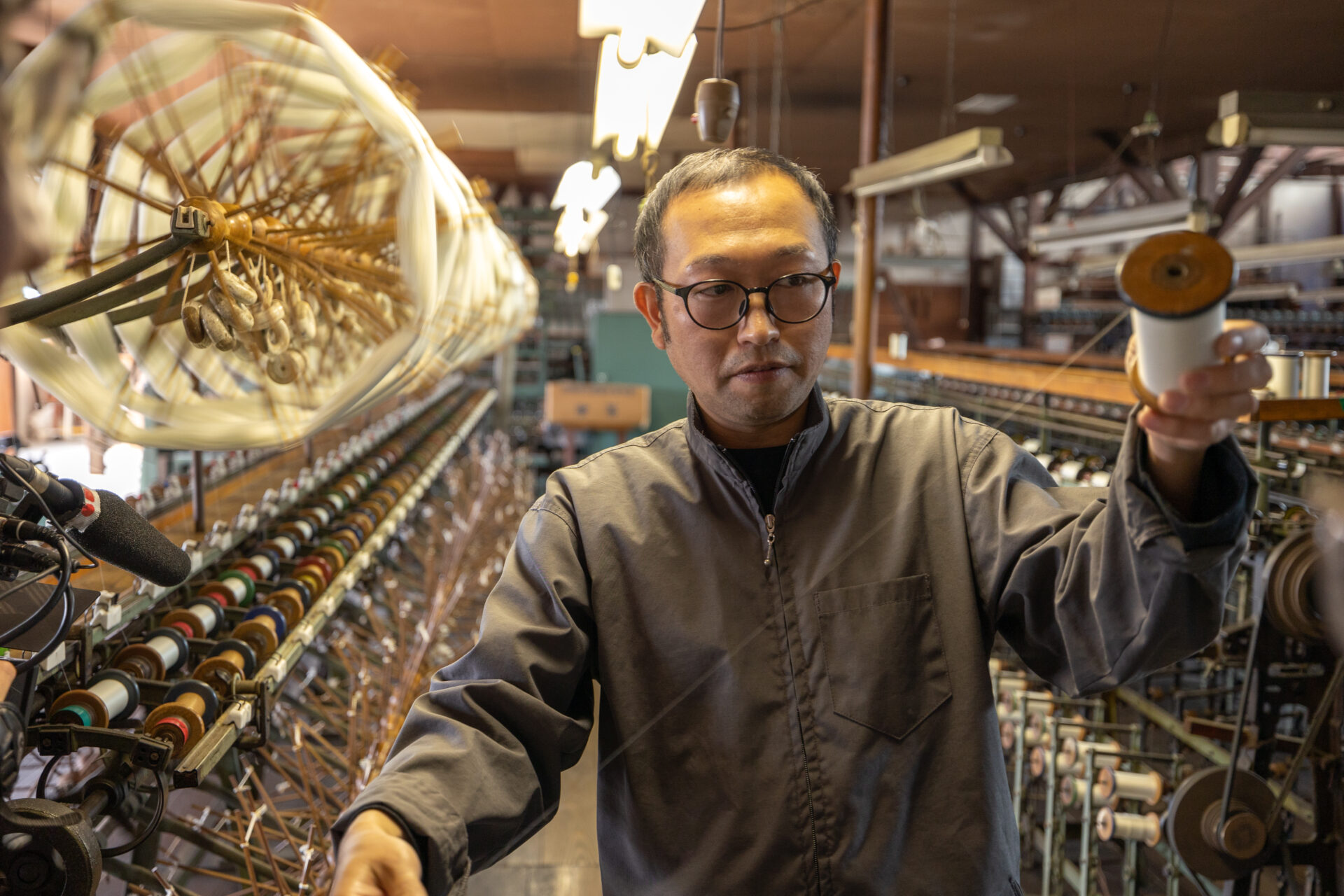
久保田 貴之
Takayuki Kubota

Komagane [Nagano]
Takayuki Kubota
A native of Nagano Prefecture and the Executive Officer of Kubota Textile Dyeing Industry Co., Ltd., the sole weaver preserving the traditional craft of "Ina Tsumugi" in the region. In addition to personally engaging in activities such as yarn production and dyeing, Mr. Kubota is actively involved in promotional efforts, participating in events to showcase the allure of Ina Tsumugi.
Located in the southern part of Nagano Prefecture, surrounded by the Southern Alps and Central Alps to the east and west, is the Ina Valley. Despite the harsh cold of Shinshu, this region enjoys a relatively mild climate, proudly boasting the highest production of mulberry trees in the prefecture. Stemming from such a background, sericulture and silk reeling flourished, earning the area the moniker " Land of silkworms, Land of silk" The silk fabric used for kimono materials, known as "Ina Tsumugi," has been designated as a nationally recognized traditional craft. With a history spanning over a century, the only remaining weaving establishment is the Kubota Textile Dyeing Industry, currently led by the fourth-generation Mr. KUBOTA Takayuki. We had the opportunity to speak with him.
Located in the southern part of Nagano Prefecture, surrounded by the Southern Alps and Central Alps to the east and west, is the Ina Valley. Despite the harsh cold of Shinshu, this region enjoys a relatively mild climate, proudly boasting the highest production of mulberry trees in the prefecture. Stemming from such a background, sericulture and silk reeling flourished, earning the area the moniker ” Land of silkworms, Land of silk” The silk fabric used for kimono materials, known as “Ina Tsumugi,” has been designated as a nationally recognized traditional craft. With a history spanning over a century, the only remaining weaving establishment is the Kubota Textile Dyeing Industry, currently led by the fourth-generation Mr. KUBOTA Takayuki. We had the opportunity to speak with him.
The sound of clattering weaving machines fills the factory. Since childhood, Mr. Kubota has been immersed in this environment.
Naturally Shouldering Over a Century of Tradition, Without Stiffness.
“My playground as a child was this factory. While all the employees were busy working, I would run around here and there. Sometimes, the lady weaving on the loom would scold me, saying, ‘You shouldn’t run so much.’ Other times, she would give me candy. Many memories are here.”
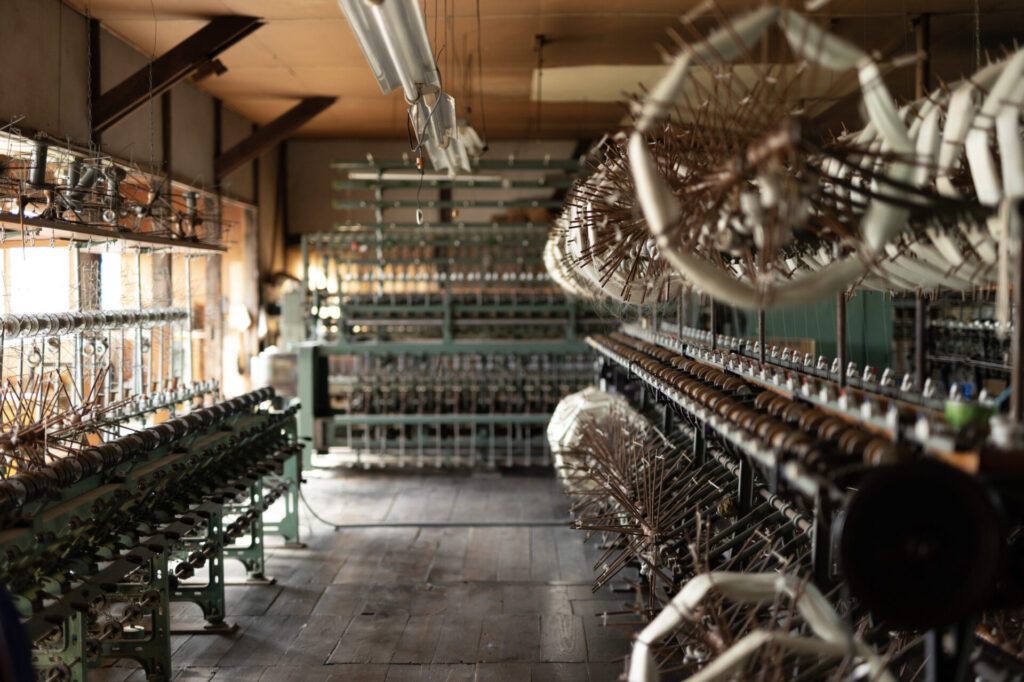
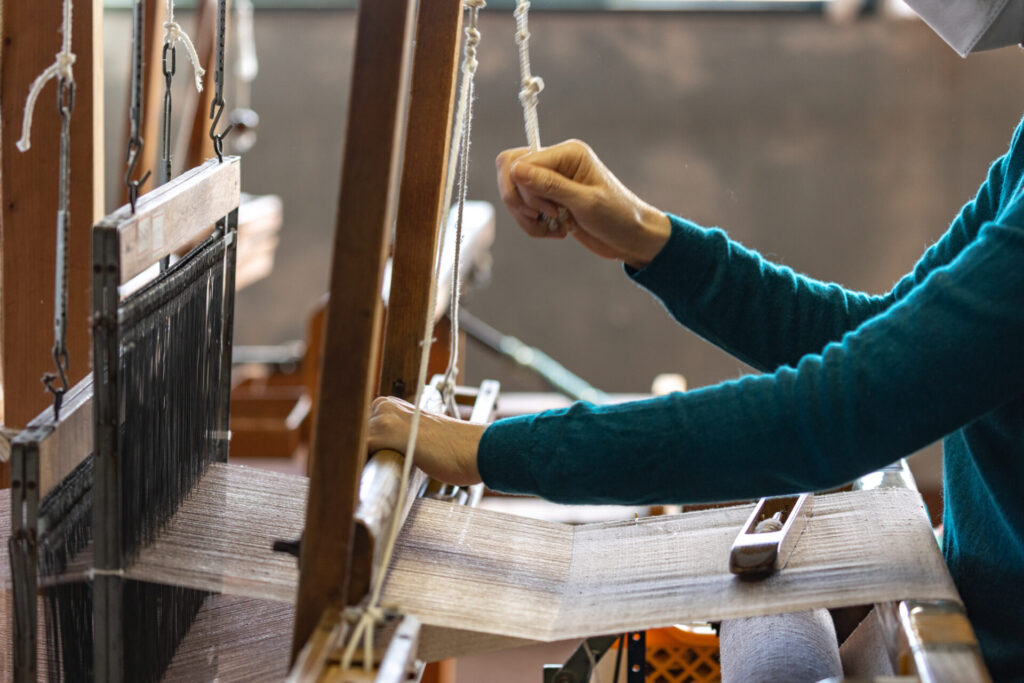
After that, Mr. Kubota left his hometown to go to university. And he entered the service industry in Tokyo.
“To be honest, I didn’t have a clear goal for the future when I started working. At the same time, I didn’t have a strong desire to inherit the family business. I was just working in a somewhat ‘go with the flow’ state.”
However, his father and the third-generation president, Mr. KUBOTA Haruhide, reached out to him, prompting him to make a U-turn.
“While I was working in Tokyo, I did have the family business in the back of my mind. But honestly, I didn’t come back with a strong determination (laughs). I entered the family business more as a natural progression than anything else.”
Without exerting pressure, he allowed himself to go with the flow. That became Mr. Kubota’s approach. He naturally took on the responsibility of inheriting a traditional weaving business with a history of over a century. Since joining the company, he has been involved in tasks such as yarn production and sales activities targeting wholesalers.
“When thinking about the next 10 or 20 years, young sensibilities are necessary. In that regard, I have expectations for my son,” says Mr. Haruhide. Currently, he supports Mr. Kubota so that he can focus on silk weaving and management. Mr. Kubota himself acknowledges that there is much to learn from his father and the previous generation.
“My father acted immediately and realized his ideas whenever he wanted to do something. I respect that aspect and feel that I need to emulate it. Recently, we’ve been challenging ourselves by attempting to create lightweight summer products within our lineup of silk fabrics, which has traditionally focused on autumn and winter items.”
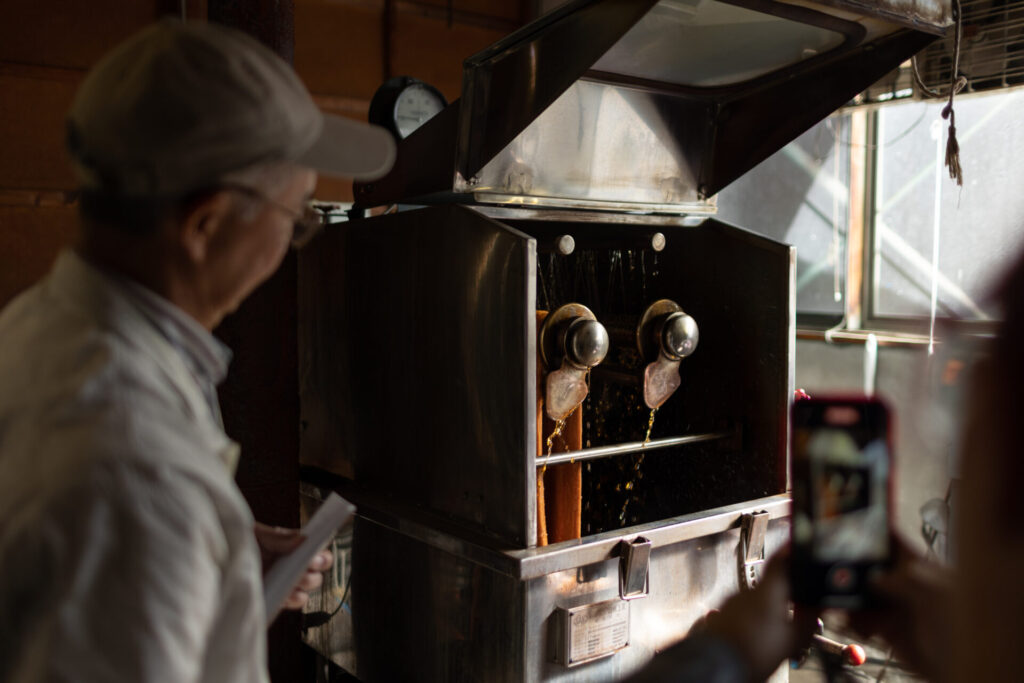
Ina Tsumugi is a traditional craft woven from the local climate and the people’s skills—a textile born of tradition.
What kind of culture does Ina Tsumugi, which Mr. Kubota and others are dedicated to, represent.
“Originally, Ina Tsumugi has its roots in fabrics woven by women for their families. During the Edo period, the encouragement of sericulture by various feudal domains in Shinshu led to the flourishing production of silkworm cocoons and silk fabrics as a supplementary occupation for farming households. Ina Valley was one of the regions where this happened. However, high-quality cocoons were shipped to urban areas such as Kyoto and Nagoya, while cocoons that were damaged by silkworms, resulting in holes, became defective and couldn’t be circulated in the market. So, women used these defective cocoons to painstakingly weave each thread on handlooms, creating fabrics for their families. That is said to be the beginning of Ina Tsumugi.”
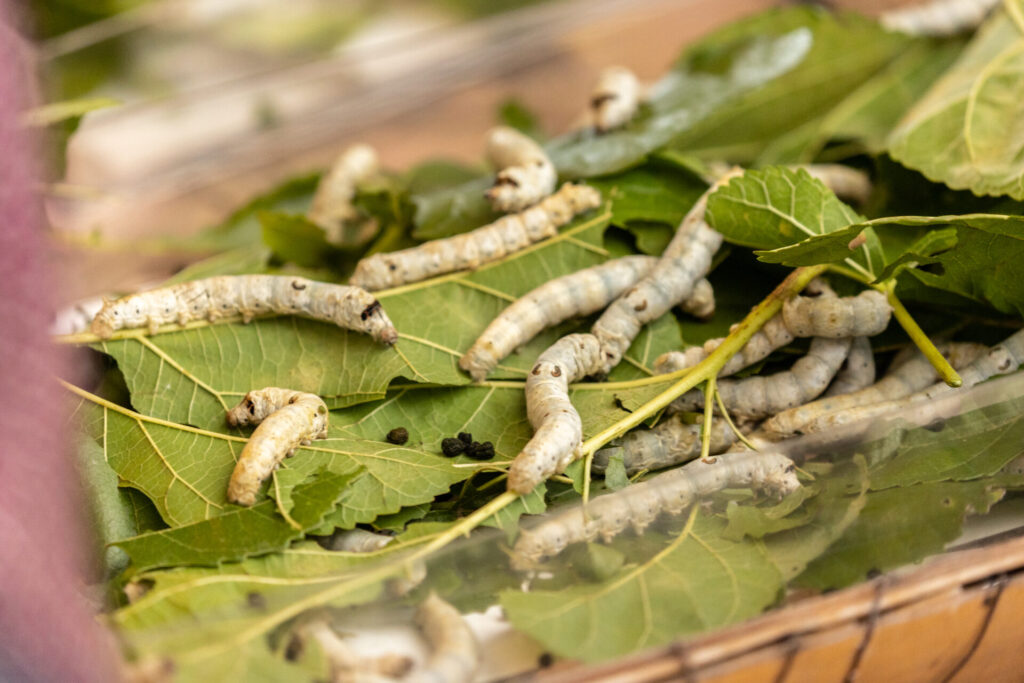
Ina Valley, situated at the foothills of the Southern Alps and Central Alps, is a naturally abundant land within Shinshu. Leveraging this geographical advantage, the technique of dyeing with natural materials, specifically plants and trees indigenous to the region, has flourished. Dyeing using materials such as yamazakura (mountain cherry) and larch, sourced from the surrounding nature, became a common practice.
“Unlike post-dyeing, where the fabric is dyed like painting on canvas, we create dyes by boiling dried materials and then dye the threads. One characteristic of yarn dyed with natural dyes is that it blends seamlessly with any other color,” says Mr. Kubota. He personally oversees the process of dyeing the threads.
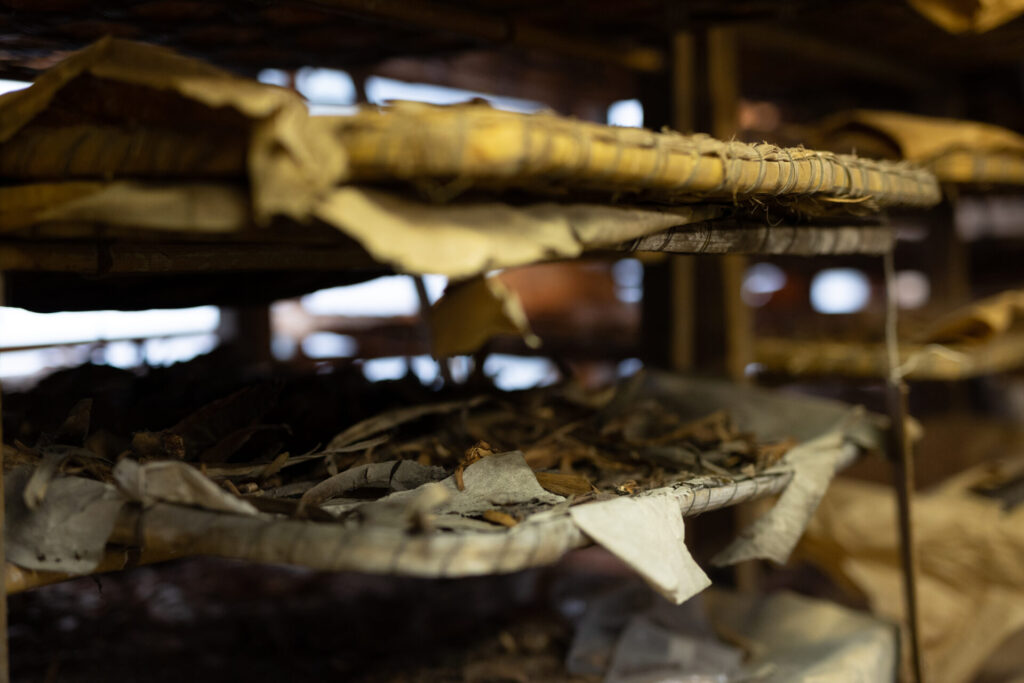
“We handle the entire manufacturing process from yarn making to dyeing and weaving. Since each item is crafted, dyed, and woven by hand, even similar patterns have a slightly different texture, which I believe adds to the charm of Ina Tsumugi.”
Rooted in the local natural environment and sustained for over a century, the silk fabric produced from this combination exudes a unique charm, embodying a soft touch, gentle texture, and a rich palette of colors.
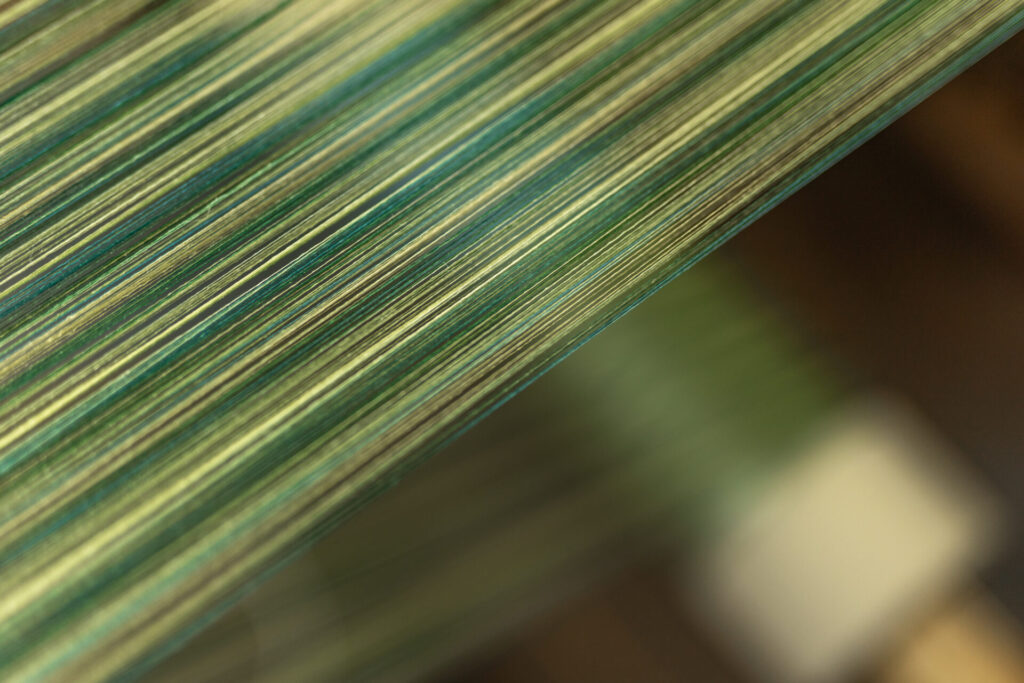
Even as times change, the desire not to let valuable traditions fade away remains strong.
Ina Tsumugi, which has conveyed the local climate and memories of the region, has been particularly valued for creating kimonos due to its beauty and texture. However, in the modern era where Westernization has advanced, the occasions for wearing kimonos have become limited. At its peak, there were reportedly over 120 factories producing Ina Tsumugi, but currently, only Mr. Kubota’s company remains. “Still…” Mr. Kubota expresses with passion.
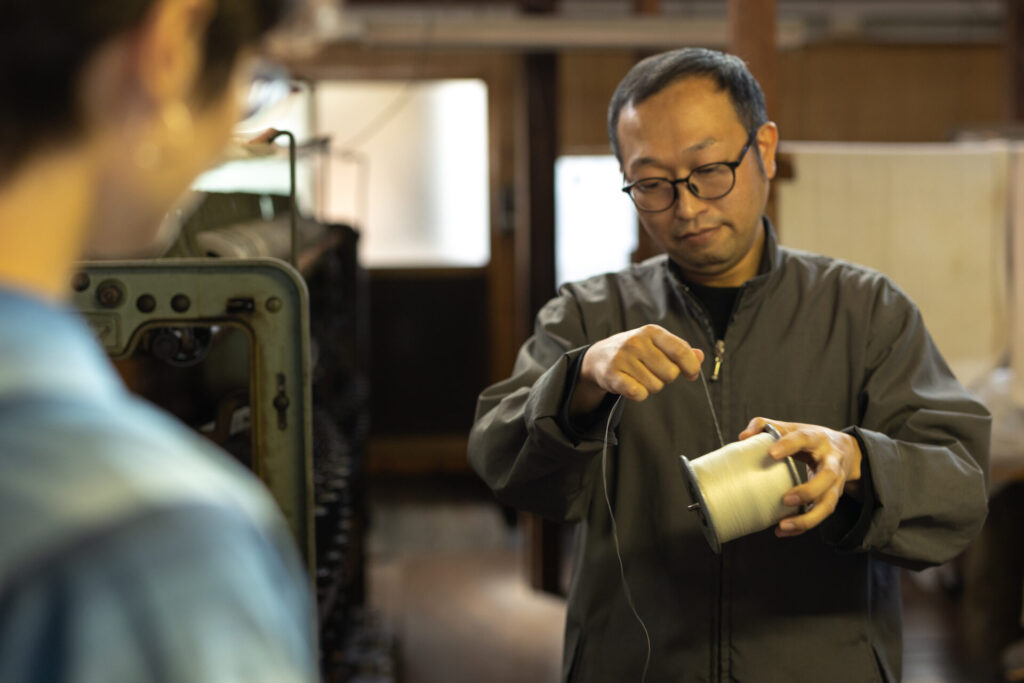
“In Japan, the kimono industry has declined since the post-war period. Now it’s a small industry, and I understand that Western clothing is certainly more convenient for daily life. It’s unlikely to return to the grand industry it once was. However, the kimono is a tradition rooted in Japan. My father often said, ‘The clothing that brings out the beauty of women and highlights the coolness of men the most is the kimono.’ I believe we must not let this history fade away. There’s no need to wear a kimono every day. Still, there is value in wearing one on celebratory occasions or events. The experiences on those days should be something special.”
Connecting Ina Tsumugi and kimono culture to the future, Mr. Kubota expresses the desire to continue taking on new challenges.
“I think the Kubota Textile Dyeing Industry has continued for over 100 years because it has adapted to the times. I can feel that identity when I see the previous generations, with the development of new products and improvements in manufacturing and dyeing techniques. We want as many people as possible to see the evolving Ina Tsumugi. Visiting our factory is more than welcome. By witnessing, learning, enjoying, and being amazed at the process of creating silk fabric, we hope to leave a lasting memory of Ina Tsumugi in people’s minds.”
Finally, I asked Mr. Kubota about what he aims to achieve in the future.
Ina Tsumugi is the result of techniques passed down from the people who have lived in this region and silk fabric born from the local surroundings. The essence of Ina Valley’s climate and memories resides within it. By evolving Ina Tsumugi, we aim to preserve this tradition and continue the legacy of the region.