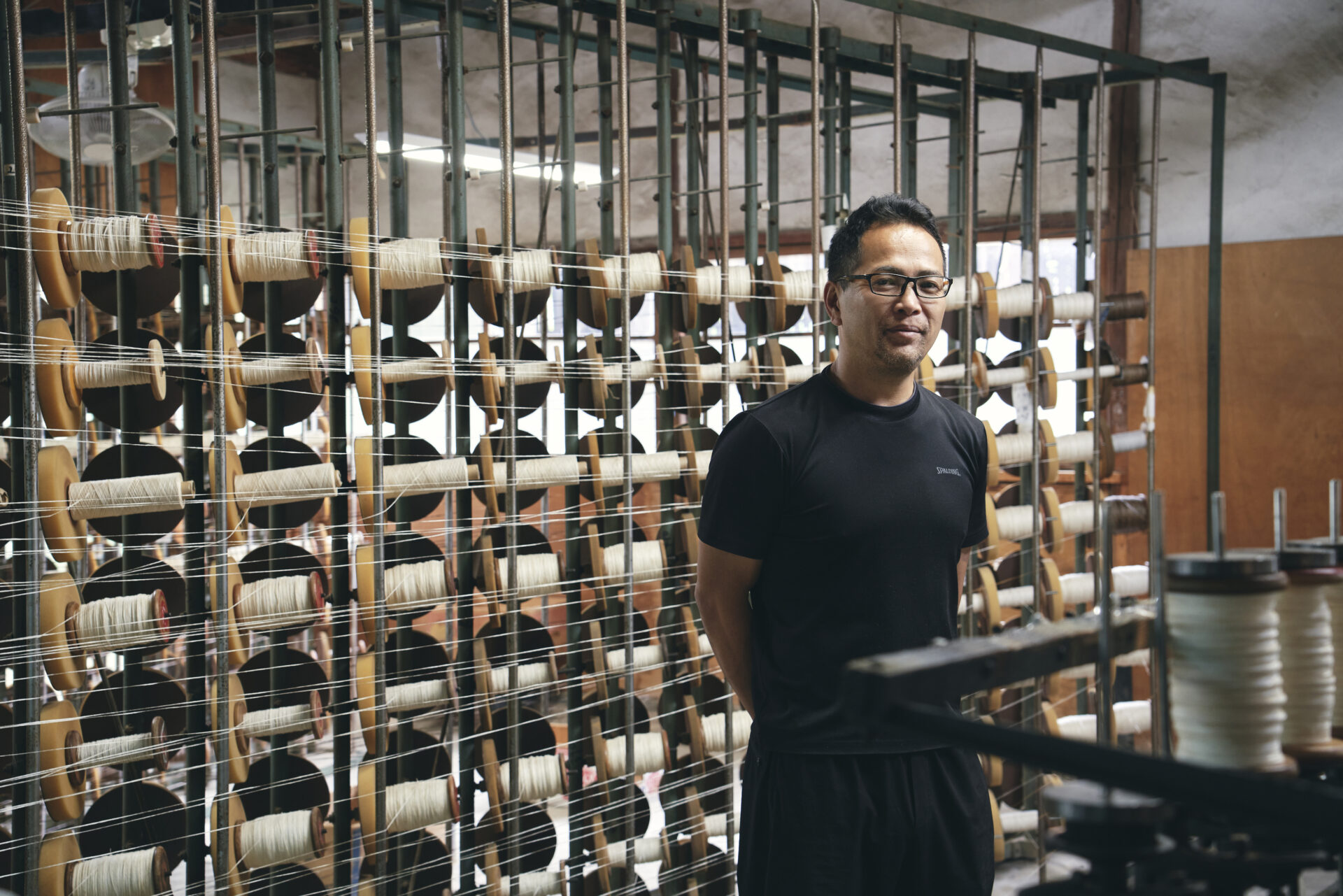
Carrying Forward Over 400 Years of Shifu Tradition to Future Generations
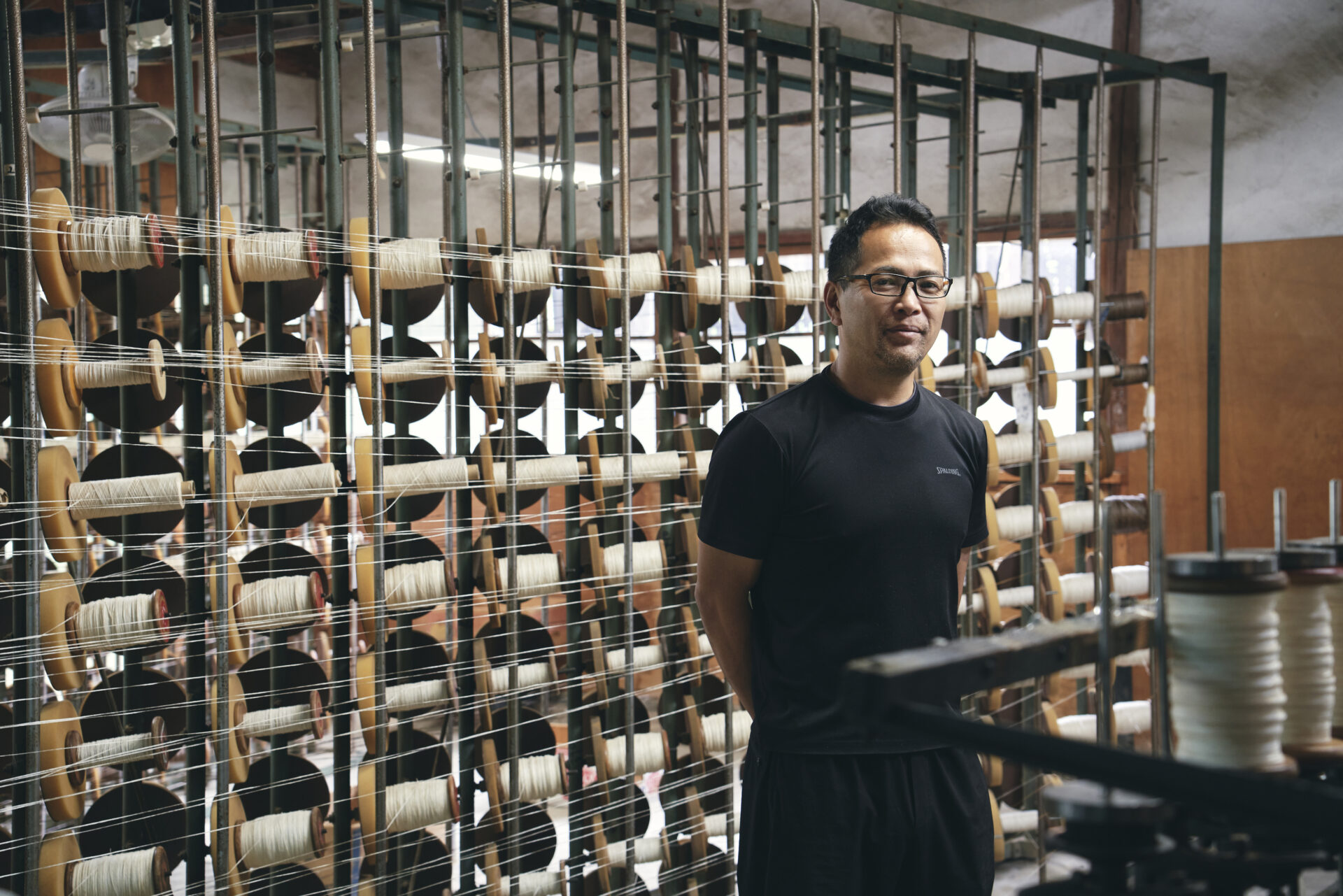
津島 久人
Hisato Tsushima

Etajima [Hiroshima]
Hisato Tsushima
A native of Nomi Island, Etajima City, Hiroshima Prefecture, Hisato Tsushima is the fifth-generation president of Tsushima Textile Manufacturing Co., Ltd. Raised in a household dedicated to the traditional craft of shifu (paper cloth), he grew up closely observing the production process. After graduating from a vocational school, he initially chose not to join the family business and instead worked as a wallpaper craftsman. However, through his work, he came to reappreciate the value of shifu, returned to his hometown, and began learning the craft under his father, the fourth-generation head. Today, in addition to producing shifu, he offers factory tours and promotes the cultural significance of the craft to a broader audience.
Shifu—a traditional fabric woven from paper—has a history of over 400 years. In Nomi Island, Etajima City, the fifth-generation head of Tsushima Textile Manufacturing Co., Ltd., Hisato Tsushima, continues this tradition. Though born into a family of traditional artisans, he once took a different path and left the island. After realizing the unique value of shifu, he returned home and inherited the family business. As the shifu industry declines with the times, Tsushima’s work is increasingly recognized for preserving and promoting this rare craft. What fuels his passion to continue making shifu for the next 100 or 200 years? Let’s explore the source of his dedication.
The Craft of Shifu, Cultivated on an Island in the Seto Inland Sea
Have you heard of shifu? As the name suggests, it’s a “cloth” (fu) woven from “paper” (shi) and is said to have a history of over 400 years. On Nomi Island in Hiroshima Bay, one of only two remaining shifu factories in Japan still carries on the tradition.
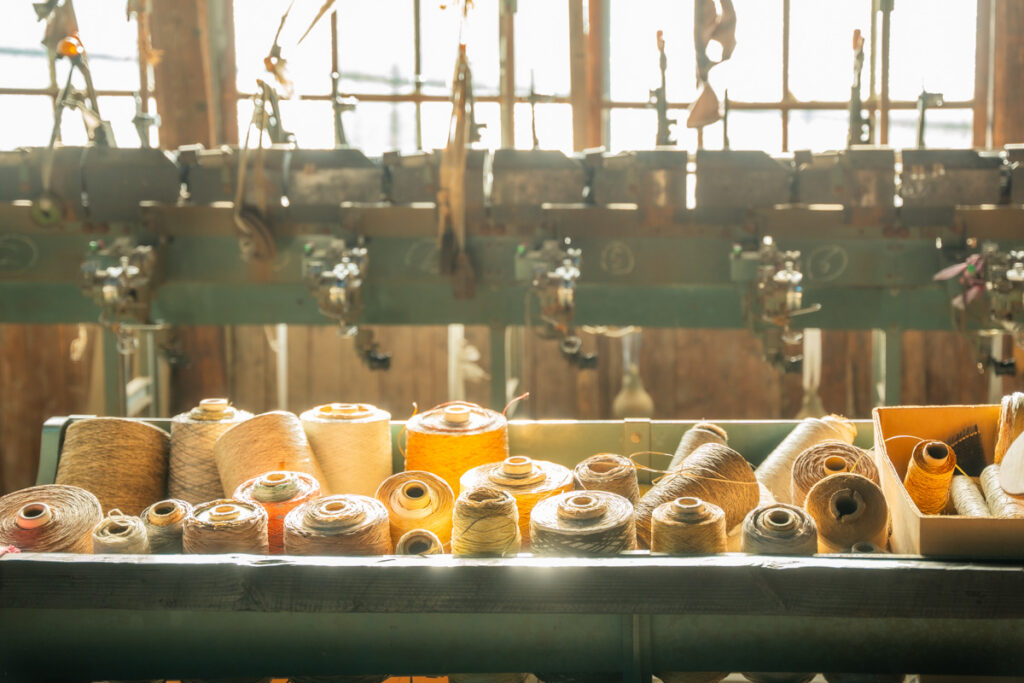
“There were once over 100 factories across the country, training many craftsmen, but as demand for shifu declined, many had to close their doors,” explains Hisato Tsushima, fifth-generation head of Tsushima Textile, founded in 1890 and devoted to textile manufacturing ever since.
Originally a cotton textile company, Tsushima Textile began producing shifu during the Showa era. Its light, supple texture made it ideal for summer kimono fabric, and it became popular in the U.S. as material for Panama hats. Inspired by this demand, Tsushima’s great-grandfather, the second-generation head, began production. Around the mid-1950s, a trading company noticed shifu’s potential as wallpaper, and it became widely used in Western interior design.
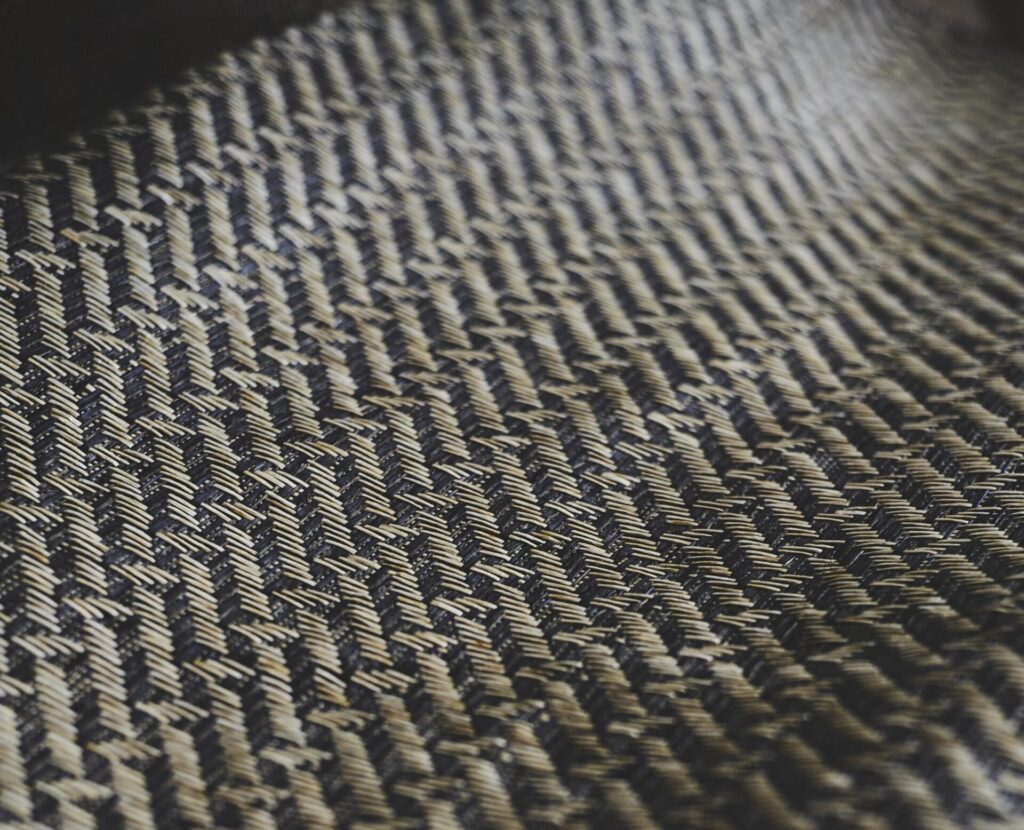
The shifu produced by Tsushima Textile uses paper made from coniferous trees. While soft and fragile in its original form, the paper is cut into strips and twisted into strong, weavable threads. These threads naturally absorb and release moisture, making them well-suited to Japan’s humid climate.
“There are old documents showing that my great-grandfather developed the technique of dyeing the threads with pigments. The fabric already had a unique and strong character, but the dyeing brought more depth and further improved its strength,” says Tsushima.
Using pigmented warp and weft threads, the fabric is woven into various patterns like checks and stripes. At its peak, Tsushima Textile produced over 500,000 meters annually, captivating customers as wallpaper. Today, 90% of its shifu is still used for wallpaper, though production has declined due to the emergence of convenient vinyl alternatives.
Leaving the Island and Returning: Embracing His Destiny as the Fifth Generation
Raised in the rich natural environment of Nomi Island, with its warm climate and expansive sea, Tsushima grew up hearing the rhythmic sounds of looms and watching shifu being made firsthand. Yet his first job was as a wallpaper craftsman—not within the family business.
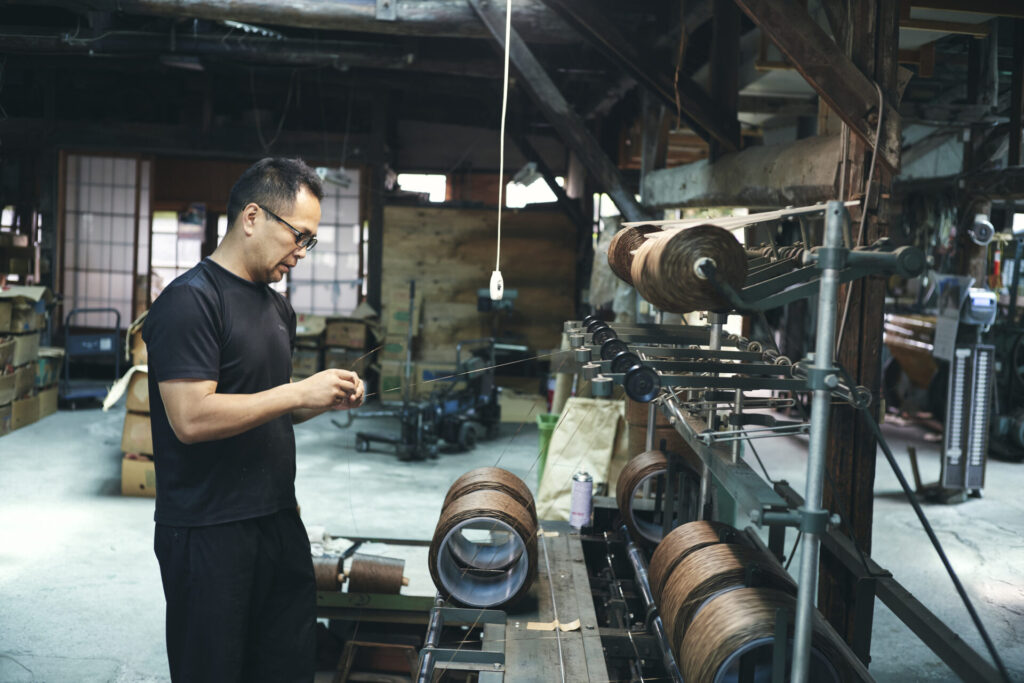
“My father never once asked me to take over the business. The only thing he told me was, ‘Learn a trade.’ So after graduation, I moved away and worked in wallpaper for about 15 years. During that time, I saw the rise of mass-produced vinyl wallpaper and began to rediscover the true value of shifu,” he says.
Eventually, he returned to Nomi Island and decided to take on the family business. For several years, he worked alongside his father.
“Seeing the level of skill involved in shifu weaving, I realized that this was something I needed to preserve. Even if demand has declined, I felt it was my fate, as the fifth generation, to carry on this one-of-a-kind tradition.”
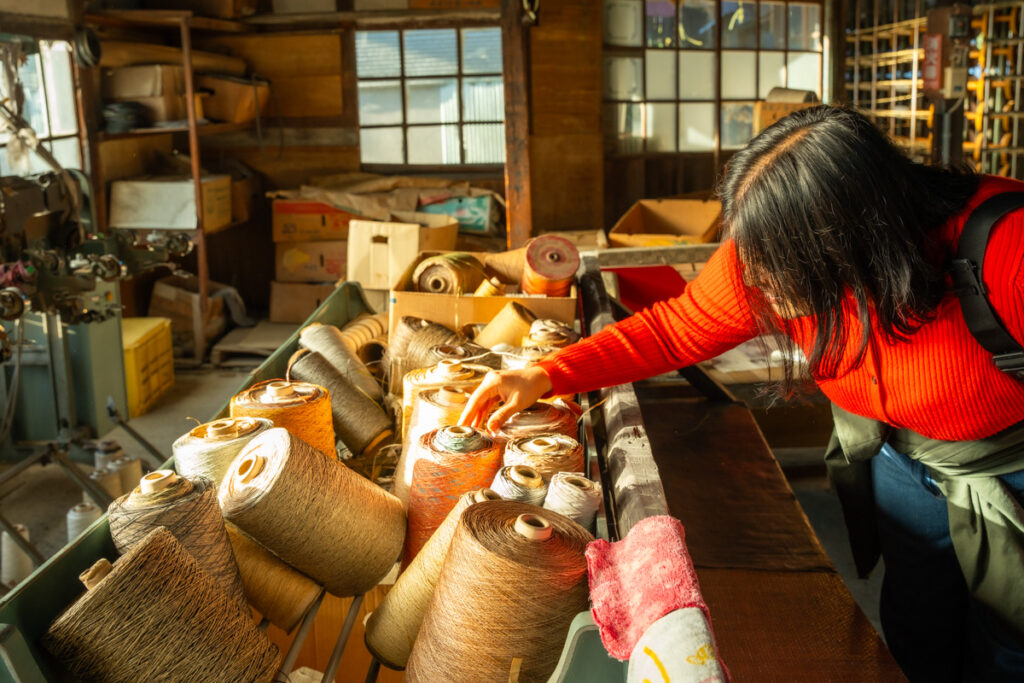
He adds, “My father was the kind of old-school craftsman who didn’t teach directly. His approach was, ‘Watch and learn.’ I was used to learning that way as a wallpaper craftsman too, so I didn’t ask many questions.”
Tsushima Textile has long held the philosophy of “feel, don’t think” when it comes to craftsmanship. With the techniques handed down since the Meiji, Taisho, and Showa eras in his blood, Tsushima responds to the subtlest changes in the factory’s air, temperature, loom movements, and sounds using his intuition.
Often, the most expressive shifu he creates aren’t the ones he plans out but those made from leftover threads woven together on a whim. Perhaps that’s the subconscious artistry passed down through generations manifesting in the fabric.
“In the warehouse next to the factory, we still have shifu woven more than 70 years ago. The patterns are stunning, and the pigment colors remain vibrant. These were likely made when we had around 50 craftsmen. The skill behind them is extraordinary. Even today, I try to replicate those designs—they’re that incredible.”
Continuing Shifu Weaving on His Native Island and Sharing Its Beauty
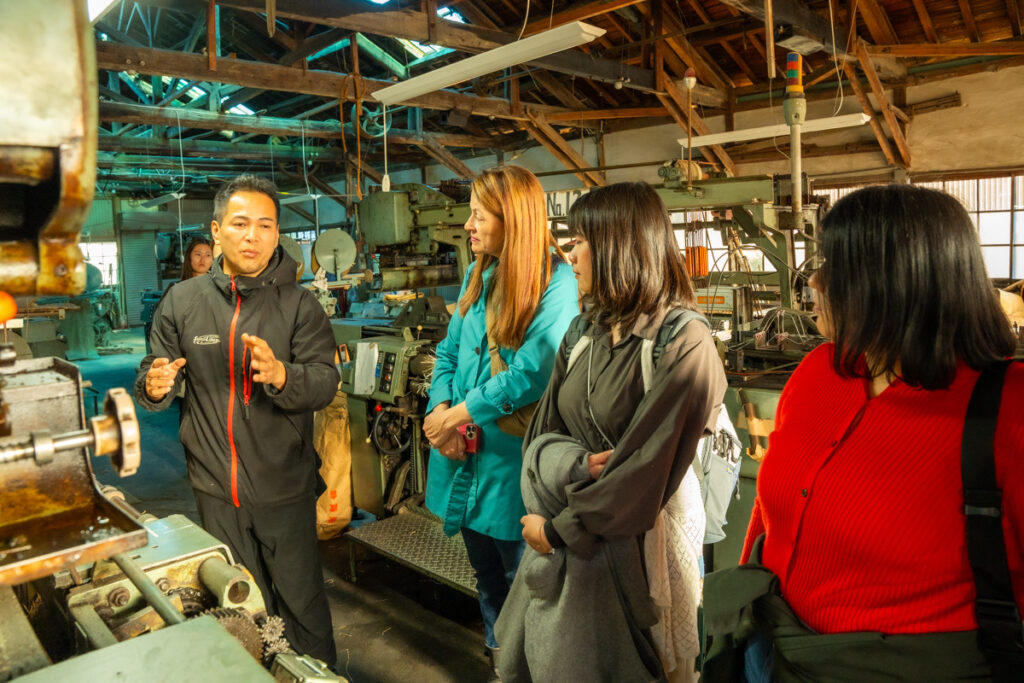
Since officially taking over the company in 2020, Tsushima has also focused on sharing shifu with wider audiences through social media. He believes it’s essential to introduce younger generations to traditional culture to ensure its survival. Factory tours and hands-on experiences are also held regularly.
During the hour-long tours, he explains shifu’s history and weaving process in detail while running the machines. Thanks to these efforts, designers and consumers from all over Japan have begun to visit.
“People are captivated watching the hundreds of warp threads being interwoven with the weft. When they touch the finished shifu, they’re moved by its texture. Some even delay their return ferry just to spend more time here. I think seeing the delicate, handmade process helps them understand the cultural value nurtured on this island.”
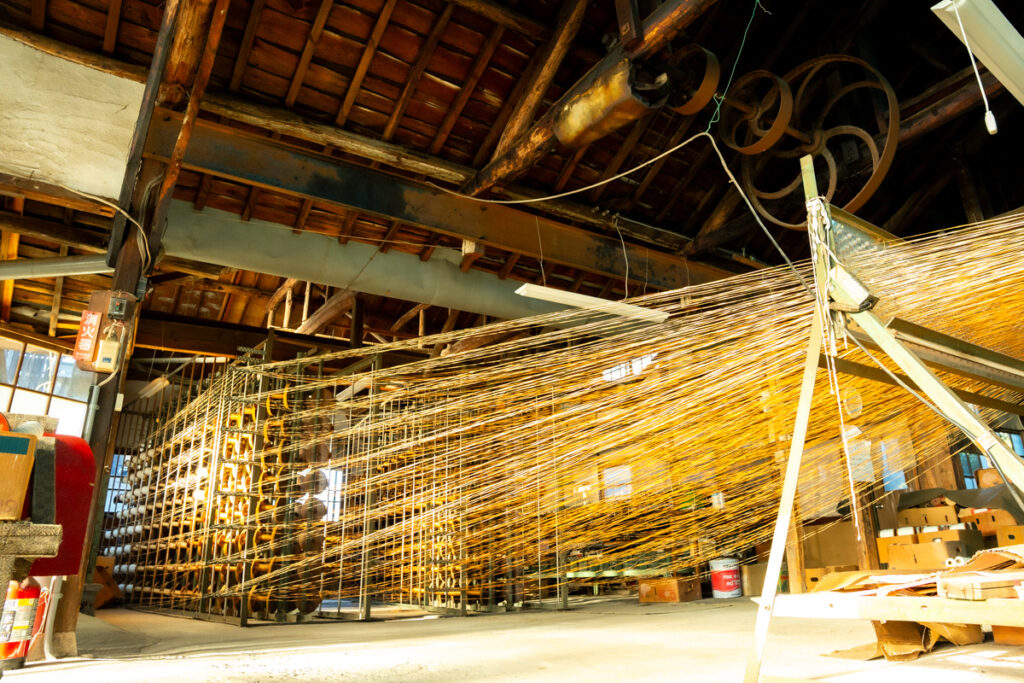
He also makes sure to emphasize that shifu is eco-friendly. Made from natural paper, it returns to the earth over time and becomes part of the soil—an organic cycle highly appreciated today. Thanks to this, along with its luxurious texture and contemporary design, shifu is increasingly being selected for high-end hotels and boutiques. Its elegant weave and design have also caught the attention of high-end handbag makers.
Tsushima actively explores product development using shifu. A shifu bag made in collaboration with a Hiroshima company won the “Regional Revitalization Award” in the 2022 Furusato Meihin of the Year. He has also developed shifu towels and coasters to offer visitors an easy way to experience its charm during factory tours.
“Even though we’ve downsized, orders from people who truly appreciate the value of authentic craftsmanship never stop. That keeps me motivated and reminds me that our environment—where real quality is still possible—is our greatest asset.”
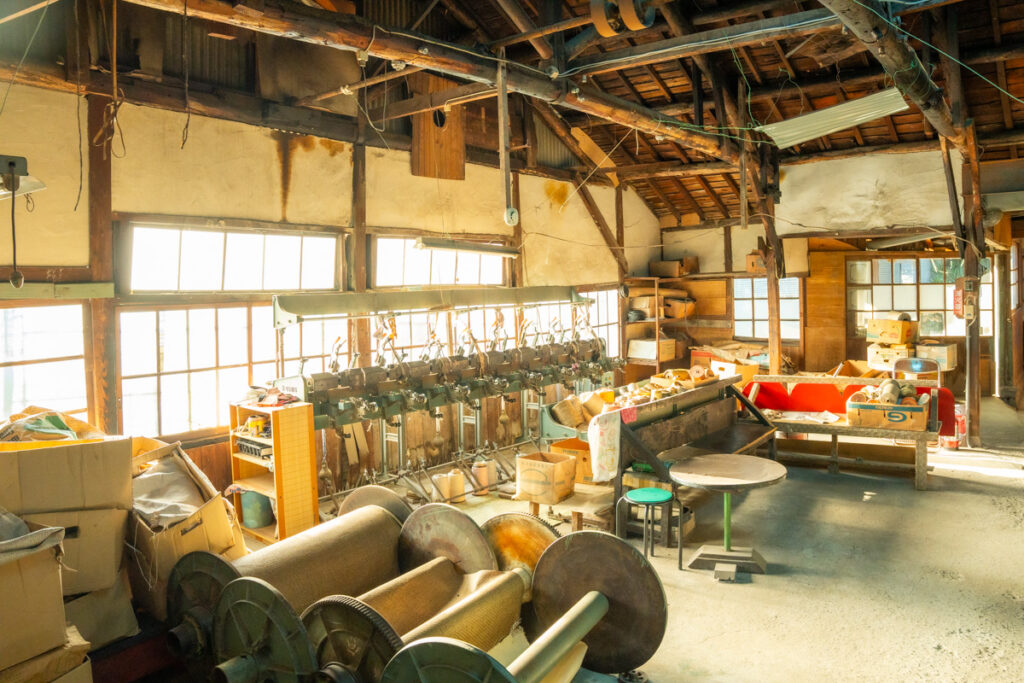
When Tsushima’s great-grandfather began producing shifu, the factory was just one of many. Now, thanks to the skills and artistry cultivated over time, shifu from Tsushima Textile is in a class of its own.
Tsushima believes this 130-year legacy was only possible because it’s been nurtured on Nomi Island.
“This island has beautiful seas and lush mountains. I believe being surrounded by nature influences our shifu production. Unlike in the city, where people and things are abundant, here you’re often alone with your thoughts. You have to make your own decisions. That solitude sharpens the senses. This is the best environment for craftsmanship. I want to continue making shifu on the island where I was born.”
What Do You Want to Pass On to the Future?
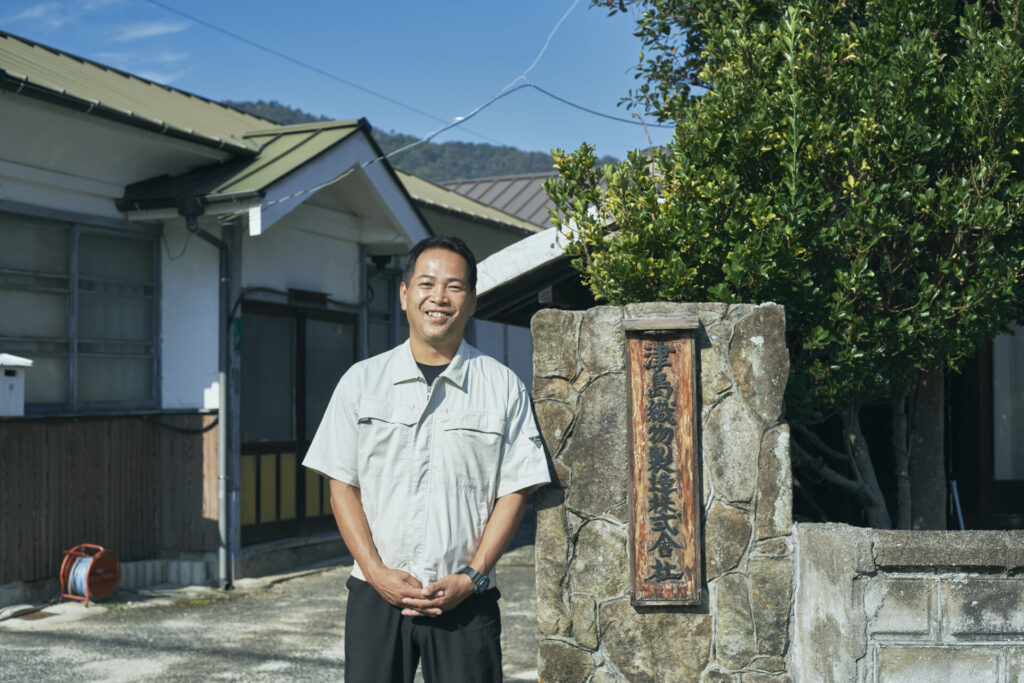
We asked Tsushima what he hopes to pass on to the next generation.
“Even if it’s just one person a day, I want more people to learn about shifu. To do that, I’ll keep planting seeds, believing that one day, they’ll bloom.”
“Leaving the island and trying another job helped me truly understand shifu’s value. Now, I strongly want to carry on this precious tradition for another 100 or 200 years. Still, with declining demand, there are fewer thread makers, and I don’t know how long production can continue. That worries me. But what I can do is stay true to my beliefs as a shifu craftsman and continue sharing its beauty with others.”Tsushima Textile has spent generations honing the skills to express the value of shifu as a form of textile art. Holding one of their creations, you can feel the passion of the ancestors and the pride of their successors. That’s the impression I took from speaking with Tsushima. Continuing a tradition is never easy—and carrying its meaning forward is even harder. Yet Tsushima radiates a quiet confidence, grounded in the undeniable legacy of craftsmanship that has been passed down through Tsushima Textile for more than a century.